Esab Caddy Tig 150 Service Manual
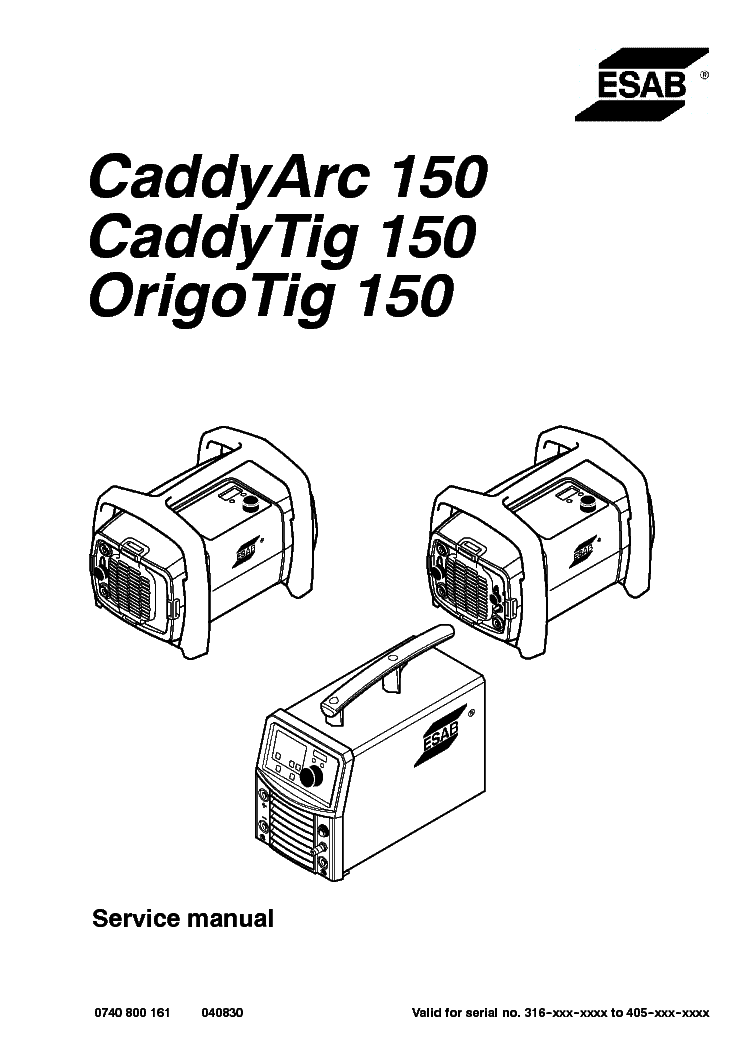
Users of ESAB equipment have the ultimate responsibility for ensuring that. Lubrication and maintenance must not be carried out on the equipment. Read and understand the instruction manual before installing or operating. 150 A / 16.0 V. 0460 450 885 Caddy Tig 2200iw, TA34 incl. Water cooler CoolMini, 3 m.
. Caddyt Arc 150i Caddyt Tig 150i Origot Tig 150i Service manual 0740 800 161 061205 Valid for serial no. 316- -xxx- -xxxx to 620- -xxx- -xxxx. READ THIS FIRST.INTRODUCTION.
Crate bx 160 manual. Louis and talked with a tech there at the plant and he actually sent me full schematics for free.
INSTRUCTIONS.SAFETY. CaddyArc 150, CaddyTig 150 and OrigoTig 150 with serial no. 316-xxx-xxxx, 328-xxx-xxxx, 341-xxx-xxxx, 405-xxx-xxxx, 613-xxx-xxxx.
Caddyt Arc 150i, Caddyt Tig 150i and Origot Tig 150i with serial no. The CaddyArc 150, CaddyTig 150, OrigoTig 150, Caddyt Arc 150i, Caddyt Tig 150i and Origot Tig 150i are designed and tested in accordance with international and European standards IEC/EN 60974. TECHNICAL DATA CaddyTig 150 OrigoTig 150 CaddyArc 150 Mains voltage 230 V ±10% 1∼ 50/60 Hz 230 V ±10% 1∼ 50/60 Hz Fuse (delayed- -action) 16 A 16 A Primary current I 36 A 36 A Primary current I 21 A 21 A Voltage/current range (TIG). WIRING DIAGRAM The power source is based on a number of function modules. These are described in the component descriptions on the following pages.
Wire numbers and component names in the wiring diagram show to which module each component belongs. Wires/cables within modules are marked 100 - 6999. Power module.
15AP1 Power board. 15AP2 Secondary board. 15C1 Smoothing capacitor, 1000 uF. 15D1 Diode module with rectifier and freewheel diodes. 15L1 Inductor.
60 mV at 100 A. 15ST1 Thermal switch, fitted in the winding of main transformer 15TM1. 15ST2 Thermal switch, fitted on the heat sink. CaddyTig 150, CaddyArc 150, OrigoTig 150 S0740 800 161/E061205/P66 -8 -ct27d1.
S0740 800 161/E061205/P66 -9 -ct27d1. DESCRIPTION OF OPERATION This description of operation describes the function of circuit boards and other components in the power source. It is divided into sections, numbered to correspond to the circuit board numbers and divisions into function blocks. 1AP1 Control panel The control board processes the control signals to/from the control panel. CaddyTig 150 Buttons Green LEDs, except D2 (yellow) GREEN LED Control panel, CaddyTig 150 S0740 800 161/E061205/P66 -11 -ct27d1. OrigoTig 150 Green LEDs, except B5 (yellow) Buttons GREEN LED Control panel, OrigoTig 150 1AP2 Display board Component positions of the display board S0740 800 161/E061205/P66 -12 -ct27d1. Circuit diagram of the display board The display segments can be tested by a service function, see pages 38 to 43.
S0740 800 161/E061205/P66 -13 -ct27d1. AP1 Power supply board The power supply board filters the mains voltage and generates internal supply voltages for the machine. 2AP1:1 Interference suppressor circuit WARNING! Dangerous voltage -mains voltage.
The mains voltage is filtered by the power supply board. Power board 15AP1 rectifies the mains voltage. Transistor Q5 is the switching element in a switched voltage supply. The secondary voltage, +24 V, is sensed by IC2 and controlled by IC1. The isolation voltage of transformer T1 and optocoupler IC3 is 4 kV. 2AP1:3 Secondary circuit The secondary circuit delivers the following voltages: +24 V The voltage is controlled by IC1 on the primary side.
2AP1 Component positions WARNING! Dangerous voltage -mains voltage. S0740 800 161/E061205/P66 -16 -ct27d2. S0740 800 161/E061205/P66 -17 -page. AP1 TIG board WARNING!
Dangerous voltage -mains voltage. The relay contacts, the gas valve 10YV1, the HF generator TR2 and the primary side of transformer TR1 are connected to 230 V mains voltage. Circuit diagram of the TIG functions of the CaddyTig and OrigoTig The processor on circuit board 20AP1 controls the HF generator and gas valve. 10AP1 Component positions WARNING! Dangerous voltage -mains voltage.
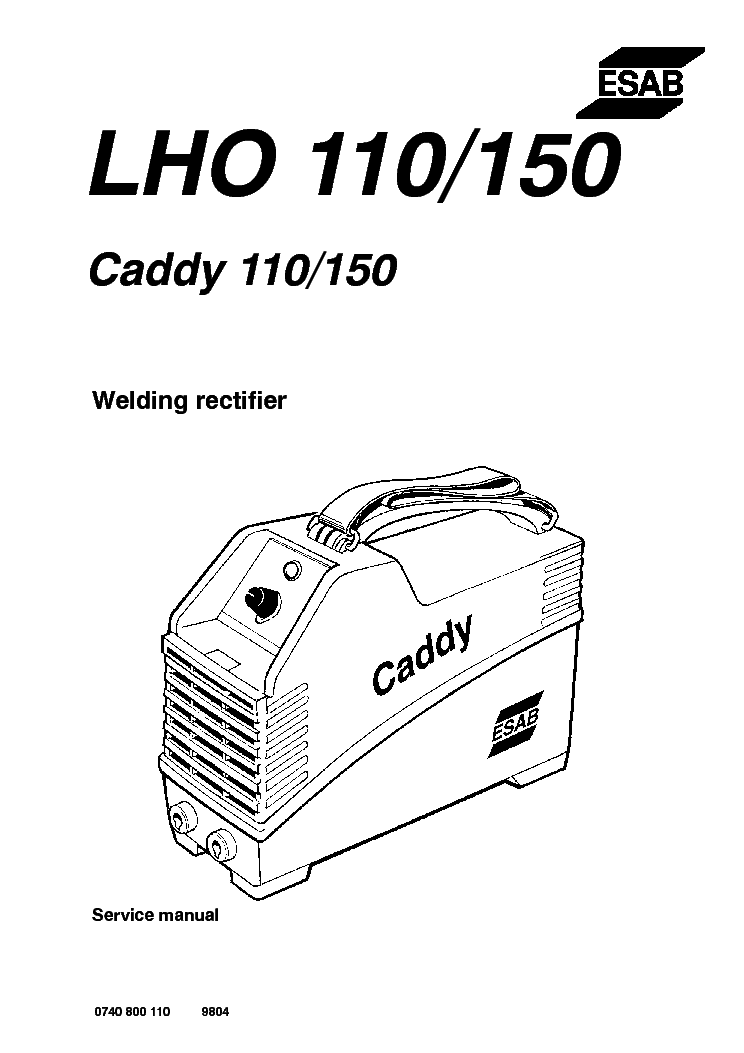
S0740 800 161/E061205/P66 -19 -ct27d10. AP1 Power board WARNING! Dangerous voltage -mains voltage.
Never make any measurements on this board when the machine is connected to the mains supply. The power module is a single forward converter, operating at a switching frequency of 65 kHz. Supply to 2AP1 The board supplies power supply board 2AP1 with 325 V DC (pins F1 and F3, connector 15XS1).
Gate driver stages Transformer TR1 is a gate driver transformer for galvanic isolation of the drive circuits from controller board 20AP1. Fuses S10 and S20 protect the gate driver circuit if the IGBT transistors fail. 15AP1 Component positions Pin positions of the semiconductor module S0740 800 161/E061205/P66 -22 -ct27d15. 15AP2 Secondary board The secondary board is fitted on the main transformer 15TM1, diode module 15D1 and inductor 15L1. Diode module 15D1 comprises two diodes, rectifier and freewheel diode. During the time interval between two voltage pulses from transformer 15TM1, the freewheel diode maintain the welding current from inductor 15L1.
AP1 Control board The processor on the control board monitors and controls the various functions of the power source. It obtains information on welding data from the control panel. If the circuit board is faulty, it must be replaced. Replacement circuit boards must be configured, see page 33. When power to the machine is turned off, the display also shows ” ” to confirm that the processor has stored the current data.
V, version 2 of 20AP1 +5 and 2. V power supply, circuit board version 2 IC6 monitors the 24 V voltage supply to the 5 V regulator on circuit board 2AP1.
-15 V The -15 V power supply is monitored by the processor. The voltage can be tested by a service function: Circuit board version 1, see service function no. 25 on page 40.
Circuit board version 2, see service function no. 18 on page 42. +10 VB Voltage regulator VR3 produces a stabilised +10 V supply, which is used to supply the remote control unit. LED display driver Version 1 of 20AP1 LED display driver, version 1 of 20AP1 The display window and the LEDs are driven by IC16, which is controlled by the processor. Version 2 of 20AP1 LED display driver, version 2 of 20AP1 The display window, the display LEDs and LEDs LED1 to LED3 are driven by transistors Q2 and Q10-Q25, which are controlled by the processor. Rotary encoder input The pulse generator on the control panel is supplied at +5 V. Pulses are supplied from the pulse generator to connections MMC18 and MMC19 with a 90 mutual phase displacement.
The pulse generator generates pulses only when its shaft is turned. Resistors R114 and R116 are pull-up resistors. Push button filters All pushbuttons are connected to 0 V, so that pressing any of them pulls down the corresponding input (MMC22 - MMC32) to 0 V. 20AP1:3 Remote control input If the remote control input is activated, but there is no reference signal, resistor R54 holds the reference input low. This results in a welding current of 3 A for TIG welding and 4 A for MMA welding.
The remote control input can be tested by a service function: Circuit board version 1, see service function no. Version 2 of circuit board 20AP1 15ST2, which is fitted on the heat sink, opens at 85 C.
15ST1, which is fitted in the winding of the main transformer, 15TM1, opens at 130 C. If either of the switches operates, the power source is stopped, a fault code is displayed and the temperature indication LED on the control panel lights. 20AP1:7 Arc voltage monitoring This circuit measures and scales the arc voltage to a suitable level for the processor. 64 V arc voltage produces a voltage signal at the cathode of diode D13, 5.1 V at version 1 of the board and 5.0 V at version 2.
When the current exceeds 10 A during welding start, the no-load voltage control is deactivated. 20AP1:9 Welding process control The processor inputs are the set values of welding data and the arc voltage. The processor also calculates a set value signal for welding current, and supplies this to the current control amplifier. The process regulator control principle Hot start MMA Peak current Adjustable starting current.
The hot start current, phase 2 above, is engaged for 240 milliseconds. It is set in per cent of the set current, but does never exceed the peak current. 20AP1:10 Machine type configuration This circuit board is used for different machines, therefore it must be configured. 20AP1 Component positions Component positions for version 1 of circuit board 20AP1 S0740 800 161/E061205/P66 -34 -ct27d20. Component positions for version 2 of circuit board 20AP1 S0740 800 161/E061205/P66 -35 -ct27d20.
Esab Caddy Tig 150 Service Manual
FAULT CODES Version 1 of circuit board 20AP1 Code Description Internal RAM fault Action: Restart the machine. If the fault persists, replace circuit board 20AP1. External RAM fault Action: Restart the machine, and then reset it. If the fault persists replace circuit board 20AP1. Version 2 of circuit board 20AP1 Code Description 5 V power supply too low The unregulated power supply voltage (+24 V) is too low: the smoothing capacitors cannot keep the voltage up enough for the processor to continue to operate. The processor stops all normal activities, expecting to be shut down. SERVICE FUNCTIONS The control panel can acess a number of service functions.
The service functions have several applications over and above service and fault tracing: those that are of importance for service and fault tracing are described here. To access the service functions: Press the welding process selection key for more than five seconds. Version 1 of circuit board 20AP1 Activate gas valve Press, the display shows “1”, the gas valve is inactive. Execute Press to activate the gas valve, the display shows “0”. Execute Press to deactivate the gas valve. Execute Press to leave this function.
Version 1 of circuit board 20AP1 25 Show - -15 V voltage Press to read the actual voltage. The display must show 98 to 120, Execute which corresponds to -13.0 to -16.0 V. Press for a new reading. Execute Press to leave this function. Version 2 of circuit board 20AP1 Quit Quit Execute Execute Select function Select function Set value Set value Show Show Keep depressed more Keep depressed more than 5 seconds to activate than 5 seconds to activate the service functions the service functions CaddyTig, control keys for the service functions CaddyArc, control keys for the service functions Select function. Version 2 of circuit board 20AP1 Deactivate the no- -load voltage control (idle control) Press, the display shows “1”, the idle control is on. Execute Press to deactivate the idle control, the display shows “0”.
Execute Press to activate the idle control. Execute Press to leave this function, the idle control is then off. Version 2 of circuit board 20AP1 21 Read / Set machine id for the MMC Press to display the actual id.
Available MMC id: Show 12 = Origo Tig 150 / Origo Tig 200 Select id by turning the selection knob. 13 = Caddy Arc 150 Press and then. The soft-starting tool SST 1 is made for the CaddyArc, CaddyTig, OrigoTig and OrigoArc. It can be ordered from ESAB, ordering no.
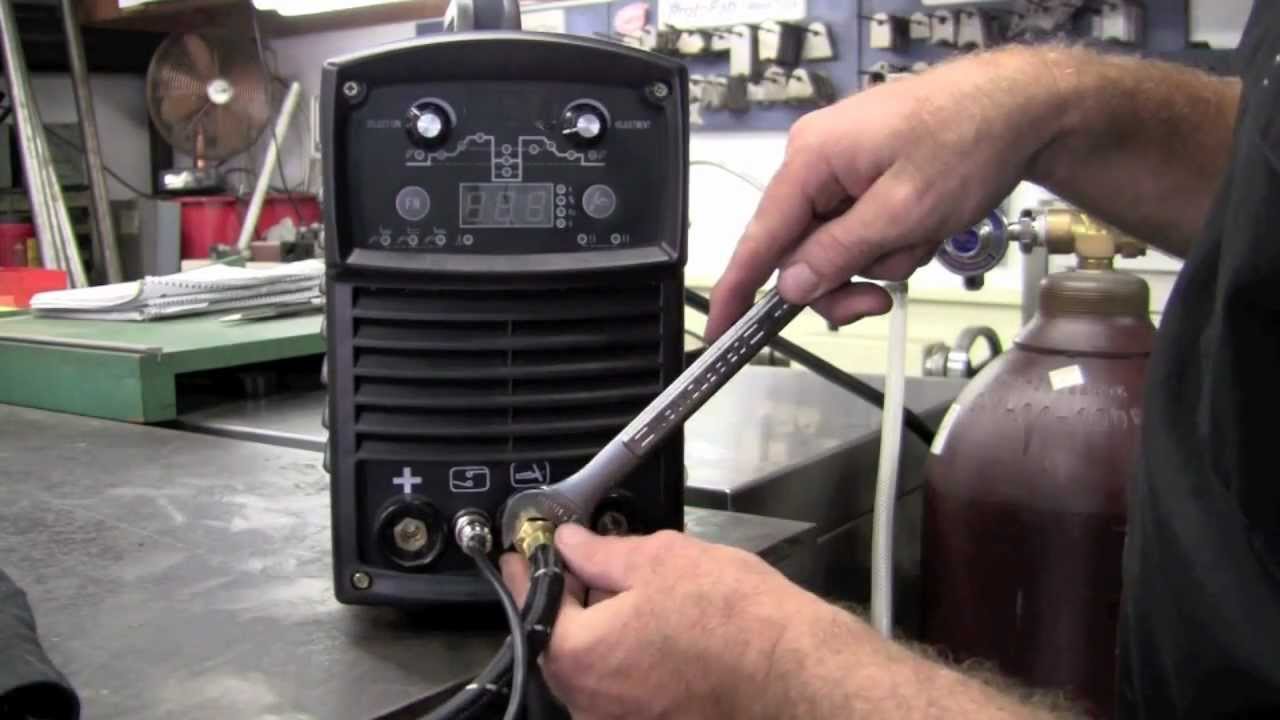
0459 534 880. The tool includes: Soft starting rectifier, cable set, voltage test board, gate pulse load and shunt voltage resistor for the OrigoArc. Dismantling CaddyArc and CaddyTig S0740 800 161/E061205/P66 -45 -ct27f3dism. Soft starting We recommend soft starting of the machine after replacing control circuit board 20AP1, power supply board 2AP1 and circuit boards or components in the power module. Soft starting supplies the power module with a low voltage in order to avoid injury to persons or damage to components. Connect the 24 V DC output of the SST 1 to terminals C1 and C2 of power board 15AP1.
Circuit connections and measuring points for soft starting 10. Switch on the machine and set it to MMA mode. Check that the DC voltage across smoothing capacitor 15C1 is 22-24 V. Checking rectifier and freewheel diodes Disconnect the machine from the mains.
Dismantle the housing of the machine. Use a Torx key no. T25 to unscrew and remove five screws from circuit board 15AP2. The screws are marked on the picture below, Bend out the circuit board so that it has no contact with the connections of the diode module. Checking the gate pulses When checking the gate pulses, the machine can either be in soft-start mode or in normal operation mode.
Special equipment To measure the gate pulses, you need a gate pulse load. This is included in soft-starting tool SST 1, which is described on page 44.
Checking the semiconductor module Rectifier diodes and thyristor IGBT transistors and freewheel diodes Measuring points for the semiconductor module Disconnect the machine from the mains and follow the instructions below. Measurements 2 - 5: Use a multimeter in diode test position to measure the diodes. Measure with the positive and negative of the multimeter connected as shown in the picture above.
Mounting components on the heat sink Thermal paste Apply thermal conducting paste to the components before fitting them to the heat sink. Start by cleaning the heat sink, and then apply a very thin, even layer of thermal paste to the contact surfaces of the components. INSTRUCTIONS This chapter is an extract from the instructions for the CaddyArc 150, CaddyTig 150 and OrigoTig 150. SAFETY WARNING!
Read and understand the instruction manual before installing or operating. INSTALLATION The installation must be executed by a professional. Placing Place the power source so that its cooling air inlets and outlets are not obstructed. CaddyArc 150 CaddyArc 150 OPERATION General safety regulations for the handling of the equipment can be found on page 52. Read through before you start using the equipment!
Connections and control devices 1. Main power supply switch 2. Mains cable 3. CaddyArc 150 MMA WELDING The CaddyArc 150 gives direct current, and you can weld most metals to alloy and non-alloy steel, stainless steel and cast iron.The CaddyArc 150 allows you to weld most coated electrodes from ∅ 1.6 to ∅ 3.25. Settings Function Setting range.
CaddyArc 150 TIG WELDING Before using the Caddy for TIG welding it must be equipped with a TIG torch and gas valve, a cylinder of argon, an argon regulator, tungsten electrodes and, if necessary, suitable filler metal. During TIG welding, the return cable must be connected to (+) and the TIG torch to (-). If they are connected in reverse, the tungsten electrode will melt. CaddyTig 150 CaddyTig 150 OPERATION General safety regulations for the handling of the equipment can be found on page 52. Read through before you start using the equipment! Connections and control devices 1.
Control panel 2. TIG: Return cable connection (+) MMA: Welding cable connection (+) 3. CaddyTig 150 Remote control unit The remote control unit has to be connected to the remote control unit socket on the machine. To activate the remote control, press the remote control symbol This is confirmed by the green LED lighting up.
Esab Tig Welding Machine
When the remote control unit is activated the control panel is deactivated. CaddyTig 150 2 stroke Functions when using 2 stroke control of the welding torch.
In the 2 stroke control mode, pressing the trigger switch starts gas pre-flow (if used) and strikes the arc (1). The current rises to the set value (as controlled by the slope up function, if in operation). CaddyTig 150 Parameter settings 1. Pulse current or continous current 3. Pulse time 4. Background current 5. Background time 6.
Slope down 7. Gas post-flow time Pulse and background time The setting range for these parameters is normally 0.01 - 2.5 seconds. However, by using micro pulse, times down to 0.001 seconds can be set. CaddyTig 150 MMA WELDING The CaddyTig 150 gives direct current, and you can weld most metals to alloy and non-alloy steel, stainless steel and cast iron. The CaddyTig 150 allows you to weld most coated electrodes from ∅ 1.6 to ∅ 3.25.
Settings Function Setting range. CaddyTig 150 WELDING DATA MEMORY Four different sets of welding data parameters can be stored in the machine’s memory: two for TIG welding and two for MMA welding. Press button for 5 seconds to store the data in the memory. At the beginning the green LED shines constantly, and then starts flashing when the data has been saved. OrigoTig 150 OrigoTig 150 OPERATION General safety regulations for the handling of the equipment can be found on page 52.
Read through before you start using the equipment! Connections and control devices 1. Mains switch 2. Connection for gas from gas bottle 3. OrigoTig 150 TIG WELDING During TIG welding, the return cable must be connected to (+) and the TIG torch to (-).
If they are connected in reverse, the tungsten electrode will melt. Settings Function Setting range In steps of Default value 2/4 stroke 2 stroke or 4 stroke 2 stroke. OrigoTig 150 LiftArct The Lift Arct function strikes the arc when the electrode is brought into contact with the workpiece and then lifted away from it. Striking the arc with the LiftArc function. Step 1: the electrode is touched on to the workpiece. Step 2: the trigger switch is pressed, and a low current starts to flow. NOTES S0740 800 161/E061205/P66 -65 -notes.
ESAB subsidiaries and representative offices Europe Asia/Pacific Representative offices NORWAY AS ESAB AUSTRIA BULGARIA CHINA Larvik ESAB Ges.m.b.H ESAB Representative Office Shanghai ESAB A/P Tel: +47 33 12 10 00 Vienna- -Liesing Sofia Shanghai Fax: +47 33 11 52 03.